中山市盈兴电子有限公司创立于2007年,拥有先进的生产设备和完善的质量管理体系,专业生产各类高频变压器,扼流圈,环型电感,绕线电感等,广泛适用于通信,电力和自动化领域(家用电器、电脑、通讯设备等)。然而由于缺少数字化的管理手段,盈兴遇到了大部分制造业工厂都会碰到的问题。
变压器的生产有一个很大的特点,就是量大。因为变压器的体积很小,一个订单多的十万起,少的也是几千几万个。
有的时候虽然是不同客户的订单,但实际产品规格一样,所以员工在生产的时候就会沿用之前客户的订单信息,不停往下做。反正是按照结算的,对工人来说多做多得,只要有物料就会一直生产下去。
然而这就会导致,
1. 不管是工人还是拉长,都不知道现在生产的到底是哪个客户哪个订单?
2. 库存积压严重,这对公司的库存和现金流来说,都产生了不小的运营压力。
变压器的生产有个特殊的地方,就是电子元器件的不良品是可以进行返修的,只有确定无法修复的产品才会变成报废品。
然而,因为员工在不断进行超量生产,根本不需要靠不良品的返修去凑数量,管理层只要看最后库存能不能支撑订单所需就够了。于是这些返修品就被随意堆放在生产线,没有人去管控这些不良品是否进行了返修,不良的原因是什么,返修成功的良品也无法计入产品数量,导致了极大的成本浪费。
同时,因为生产数据缺失,车间信息不透明,拉长根本无法对不良品的损耗和不良品的原因进行统计分析。结果就是,拉长每天都很忙,花费很多时间做数据统计,但“数”到用时方恨少,想要的数据要么没有,要么是滞后的,根本无法进行管理优化。
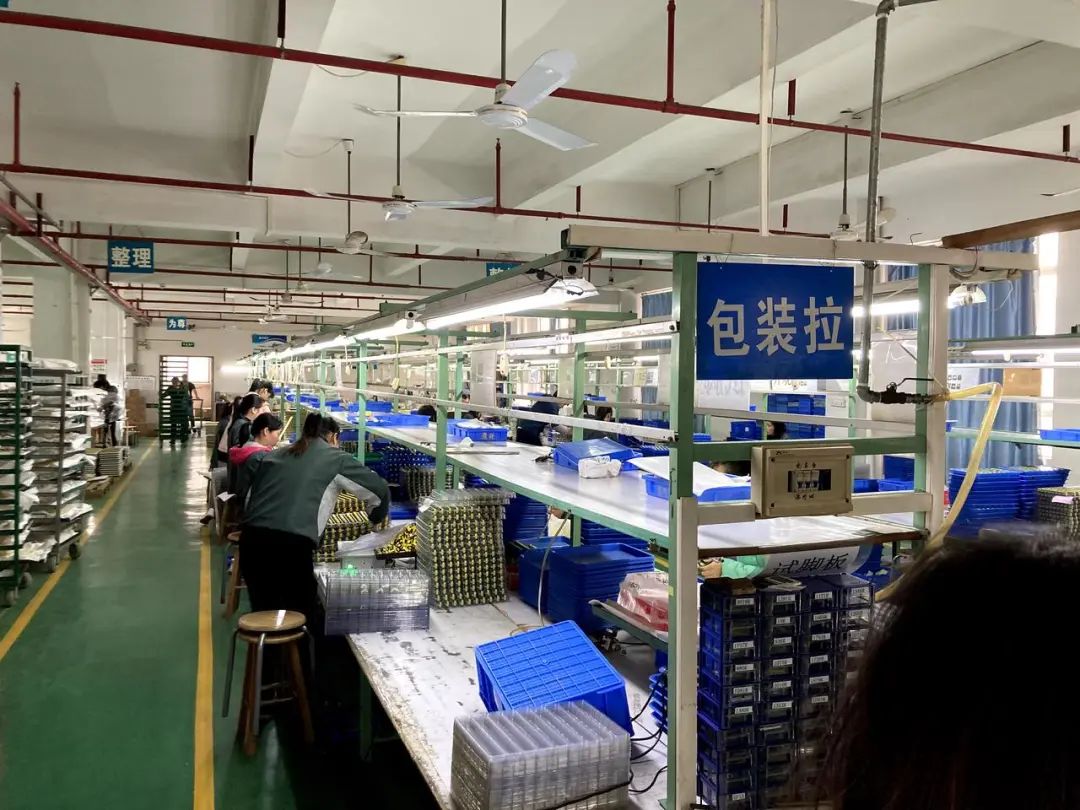
于是肖厂长开始考虑,要怎么才能改变这个现状。
直到无意中看到了的广告,只要几千块钱,上线也很快,肖厂长觉得很有意思,当场就拍板下单了。“现在我们已经用了半年了,确实解决了我们很大的困扰。”
——肖厂长
首先最重要的是有实时细颗粒度的数据了,及时、准确、清晰、有效。
用电子工单替代原先的纸质工单,每道工序都进行产出报工,这样工人到底在做哪个订单?这个订单进行到哪一道工序了?需要做多少件、已经做了多少件、还需要多少件?在小工单的系统里清清楚楚就能看到,再也不需要拉长辛辛苦苦去收集、汇总、统计。
如果有哪道工序多报工了,拉长也能很快就知道,并且去现场核查是什么原因,是多报工还是多生产?多生产的话下道工序是否接收了同等数量的产品?这样一天就可以节省拉长们起码三小时的时间,去做更有效率和价值的事情,比如对不良品进行精细化的管控。
有了实时准确的数据,管理层就有依据去对不良品和报废品进行管控。
员工在报工时填写不良品项原因,生产主管就可以分析,到底是操作问题还是材料问题,从而提出针对型解决方案,是提供操作培训,还是需要更换原材料,来达到降低不良品率的目的。需要返修的不良品也能进行严格的管控,返修成功的不良品及时汇入良品统计,极大地降低损耗,节约成本。
“对我而言,最直观的感受是,客户的评价反馈更积极了。即使晚上收到客户的消息,我也可以通过小工单很快的掌握生产进度,查询出货状态,然后及时的同步给客户。”
——肖厂长
盈兴电子在使用「」后,生产效率提高了、生产成本降低了、客户满意度提升了,最终表现出来的就是公司实际效益和利润的提升。如果您也遇到了生产管理难题,就扫描下方二维码咨询解决方案吧!